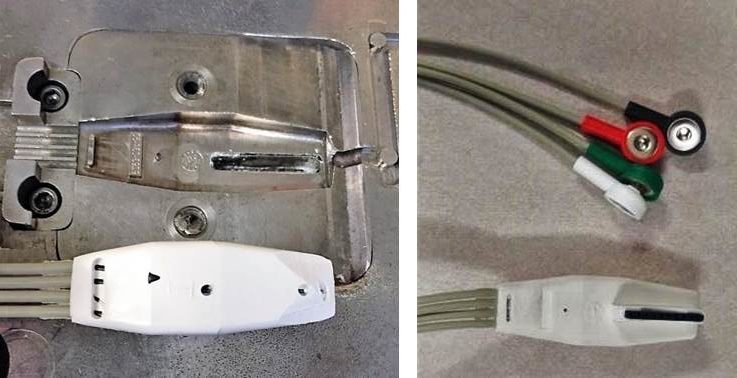
When OEM’s outsource their overmolding needs to Axcesor for manufacturing and assembly, the entire product production process undergoes a review to insure that the finished product meets production cost targets and stringent quality standards.
In the case of an ECG overmolded cable assembly, the pre-shot and overmold tools were worn conventional molds that were run on an obsolete shuttle machine. Additionally, the molds had deteriorated to such an extent that shims were required to keep the insert in position. The process was inefficient: it required a lot of post trimming after the pre-shot in order to prevent breakouts in the overmold, and the scrap rate was excessive.
To improve the production process, the molds were converted to book style molds to run on Axcesor’s state of the art vertical presses.
Book molding is a very efficient process in which the base of the mold is mounted on top of a rotary table used to position and present a series of molds to a molding station. Some of the benefits of this method include:
- A more secure positioning of the insert
- Molded parts cure in the mold during travel, giving faster cycles and higher yields
- Multiple molds on a rotary table give the fastest cycles and highest possible yields
- Low volume production can begin with just one Book Mold, and production can be easily expanded by adding more molds later
- Book Molds typically cost less than conventional molds cavity for cavity
The mold cavities were welded up, re-machined and polished, and pins were added to hold the part in place. Gates were re-done for better material flow.
Thanks to a complete rethinking of the original production process our comprehensive subcontract manufacturing review has eliminated the high scrap, and allowed our customer to divest their shuttle machine and open the space for other needs. In addition, the quality and dimensional consistency of the finished parts has been improved.